3D printing at Horn
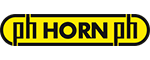

Horn launched its additive manufacturing project in spring 2018, which led to the creation of a dedicated “selective laser melting” production area. The tool manufacturer uses additive manufacturing to produce its own tools – particularly prototypes, special tools and tool holders – and to optimise coolant attachments. Having recognised the advanced possibilities offered by additive manufacturing, Horn is making these available to its customers and partners as well.
Matthias Rommel, Managing Director of Paul Horn GmbH says, “We were captivated by additive manufacturing right from the start and so we kept a very close eye on advances in the area of 3D metal printing. As soon as the technology had matured to the point where we could use it to manufacture precision tools, we bought our very first system. Originally, we purchased the machine for the R&D area so that we could make special tools and prototypes. During the initial period, we found that we were constantly having discussions with our customers about 3D printing. To begin with, these were purely technical but as time went by they led to more and more concrete enquiries for 3D-printed components. Due to the strong interest from customers, we eventually came up with the idea of setting up an additional contract manufacturing business unit for additively manufactured components. In terms of technology, we opted for a DMG Mori LASERTEC 30 (2nd generation)."
It makes sense to use additive manufacturing if it generates a technological advantage. However, in many cases there is no economic benefit to using additive manufacturing for a component that used to be produced by conventional methods. One example would be a turned part that can be produced relatively quickly on a Swiss-type lathe. Not only that, but additive manufacturing would also be too expensive in terms of post-processing. Other disadvantages compared to conventional production include relatively poor surface quality (Rz 30 µm), accuracies down to only +/-0.1 mm and the high cost of powder compared to bar.
Greater design freedom
As the complexity of a component begins to rise, additive manufacturing becomes more relevant. This may be driven by the need for lightweight design, special cooling channel layouts and small batches of components with highly complex geometry. Consequently, the disadvantages have to be weighed against the benefits of greater design freedom, lightweight construction, quick adaptability and speedier production for more complex parts. In the future, it therefore makes sense for this option to be included in the preliminary considerations as part of each design process.
The specialists analyse the raw material from various perspectives. During this process, Horn draws on the extensive expertise of Horn Hartstoffe GmbH, which has been analysing carbide powders for years. The required measuring equipment is therefore already available. If the input parameters are OK, test pieces are printed which undergo metallurgical analysis. To ensure that data is generated quickly, we rely on both Horn Hartstoffe and the new Horn analysis centre (HAZ). It is here that employees create suitable micrographs for analysing pores and conduct further material tests.
From unfinished parts to finished components
Horn uses the selective laser melting process, which is also known as laser powder bed fusion. In this technique, metal powder is spread over a platform in a thin layer and the relevant area is targeted and melted by the laser. The platform is lowered in small increments and the process is repeated until the required component height has been achieved. By way of materials, Horn uses aluminium (AlSi10Mg), stainless steel (1.4404), tool steel (1.2709) and titanium (Ti6Al4V). However, other materials are currently being tested. The maximum build volume is 300 x 300 x 300 mm.
As Horn keeps all production stages in-house, the specialists within the production area are able to respond to customer requirements directly. The parts are produced in various designs according to customers’ wishes. Horn also assists customers with the design process and with the selection of appropriate powder-based parameters. Depending on what customers require, Horn can produce everything from unfinished parts right through to finished components. Another advantage is the ability to make use of available machinery and measuring equipment. This saves time and has a direct impact on all production processes.
Example: printed coolant attachments
Paul Horn GmbH offers additively manufactured coolant discs that are produced to meet customer requirements, facilitating reliable chip control during high-performance reaming. Reaming through-holes or deep blind holes often presents a technical stumbling block for conventional machining solutions. Long-chipping materials and materials that are difficult to machine make it necessary to modify the tool system as well as the internal coolant supply. Horn has developed a solution to this problem with its 3D-printed coolant disc that can be screwed onto the tool shank. It results in extended tool life due to the direct, targeted cooling and, above all, reliable chip removal. Additive manufacturing technology enables the coolant outlets to be designed freely. The form of the outlets prevents chips from getting inside. Furthermore, the cross-section and exit angle of the cooling channel can be adapted to suit the specific machining task and material to be machined.