Hochkarätige Werkzeuge für höchste Ansprüche
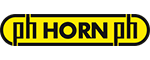

„Wer einmal auf einem Virus Brett stand - der weiß: diese Bretter machen süchtig“, scherzt Frank Dietzel. Der Geschäftsführer der Virus Sportartikel GmbH produziert in seiner Manufaktur seit über 30 Jahren Highend Snowboards und Skier für Wintersportler mit höchsten Ansprüchen. Zusammen mit seinem Team setzt Dietzel bei der Herstellung auf Hightech-Faserverbundwerkstoffe und heimische Hölzer. „In jedem unserer Bretter steckt ein flexibler Holzkern“, erklärt Dietzel. Neben viel Handarbeit kommt für die Zuschnitte der CFK-Matten und dem Fräsen von Holzkernen eine CNC-Fräsmaschine zum Einsatz. Hier setzen die Spezialisten auf Diamantwerkzeuge der Tübinger Paul Horn GmbH.
Als der Snowboardsport im Jahr 1984 noch in den Kinderschuhen steckte, begann Dietzel in Großwallstadt schon mit der professionellen Produktion dieser neuartigen Wintersportgeräte. Seither gilt die Marke Virus als feste Größe in der Branche. Profis und anspruchsvolle Wintersportler setzen auf die Performance der Snowboards und Skier. Virus Boards sind aus Hightech-Werkstoffen in Verbindung mit Vollholzkernen als Sandwich-Bauweise hergestellt. Die Holzkerne entstehen durch reine Handarbeit und sind je nach Modell mit zwei bis drei Carboneinlagen verstärkt. Dietzel setzt für seine Top-Modelle auch auf den Werkstoff Zylon. Hierbei handelt es sich um die stärkste Faser, die je von Menschenhand produziert wurde. „Zylon ist wie eine künstliche Spinnenfaser, die eine viel höhere Reißfestigkeit als Carbon aufweist. Die Verarbeitung ist sehr aufwändig und erfordert besondere Werkzeuge und Technologien, um diese Faser überhaupt schneiden zu können“, so Dietzel.
Die einzelnen Schichten der Sandwich-Bauweise haben unterschiedliche Aufgaben. Der Kern bestimmt den Großteil der Eigenschaften des fertigen Bretts. Aufgrund der allround Eigenschaften ist Holz ein sehr gutes Kernmaterial. Ein Holzkern besteht aus mehreren miteinander verklebten Streifen von laminierten Harthölzern. Sie bieten einen natürlichen Flex des Boards und verfügen über eine gute Vibrationsdämpfung. Um gewisse Bereiche des Bretts zu verstärken, sind Einlagen aus Karbon und Glasfaser in das Laminat eingebracht. Die Sportgeräte müssen sich in schnellen Kurvenfahrten dem Untergrund anpassen, aber beim Lastwechsel sich schnell wieder in Ausgangsform zurückbiegen. Wichtig ist hierbei, dass das Material nicht wie eine Sprungfeder reagiert, was die Kontrolle sehr beeinflussen würde. Dietzel laminiert CFK-Matten in den Kern und in die äußere Schicht, was das Handling und die Performance des Sportgeräts nochmal deutlich steigert.
CVD-Diamant
Für den Zuschnitt der CFK-Matten sowie beim Fräsen der Holzkerne setzt Dietzel auf CVD-Diamant bestückte sowie CVD-Diamant beschichtete Fräswerkzeuge von Horn und eine CNC-Portalfräsmaschine. „Die Werkstoffe wirken sehr abrasiv. Hartmetall würde bei der Bearbeitung zu schnell verschleißen“, sagt der Außendienstmitarbeiter von Horn, Stefan Bachmann. Für das Fräsen der CFK-Matten und der 3D-Formen der Holzkerne kommen diamantbeschichtete Schaftfräser des Typs DSS zum Einsatz. Zum Besäumen von Flanken ein bestückter CVD-D Fräser mit fünf Schneiden.
„Sehr wichtig sind die Kanten der CFK-Matten. Wenn diese ausgefranste oder delaminierte Stellen aufweisen, sind sie unbrauchbar. Die Leistung der Fräswerkzeuge von Horn stellen uns voll zufrieden, denn Ausschuss ist bei CFK sehr teuer“, erklärt Dietzel. Auf den CFK-Matten ist für die Fräsbearbeitung noch ein zusätzliches Gewebe aufgeklebt, welches zum Schutz der Kanten dient. Dieses Gewebe wird nach der Bearbeitung abgezogen. Dietzel setzt für die Fräsbearbeitungen auf einer CNC-Portalfräsmaschine, welche normalerweise in der Holzindustrie Möbelteile bearbeitet. „Die Maschine mit dem Vakuumspanntisch bietet uns alle Voraussetzungen und Bearbeitungsmöglichkeiten, die wir für unsere Produkte benötigen“, erklärt der Geschäftsführer.
Schneiden statt quetschen
CVD-Diamant Schneiden unterscheiden sich mehrfach von PKD-Schneiden. Der CVD-Diamant ist zu 99,99 Prozent fast reiner Diamant im Gegensatz zum mit Binderanteilen von 10 bis 20 Prozent gemischten PKD. Obwohl beide Schneidstoffe polykristallin aufgebaut sind, ist die Struktur von CVD-Diamant homogener und fast ebenso hart und verschleißfest wie monokristalliner Naturdiamant. Während PKD-Schneiden üblicherweise geschliffen oder erodiert werden, sind CVD-Schneiden präzisionsgelasert und damit mit einer Schneidenverrundung zwischen einem und zwei µm mindestens zehnmal so scharf. Beim Schleifen von PKD werden Randkristalle an der Schneide herausgebrochen, beim Lasern von CVD-Diamanten aber durchschnitten. Dadurch erklärt sich auch die hohe Standmenge beim Bearbeiten von kohlefaser- und glasfaserverstärkten Kunststoffen. Mit einer Schneidkantenschärfe von 1 bis 2 µm durchschneiden die CVD-Diamant-Schneiden die 5 bis 8 µm dünnen Fasern, während die PKD-Schneiden mit ihrer zehnfachen Schneidkantenverrundung die Fasern lediglich abquetschen und durch Reibung schneller verschleißen.