Am 20.09.2017 fand in Hannover das Symposium „Chancen und Perspektiven additiver Fertigung“ statt. Sechs Referenten aus dem Mitgliederkreis der VDMA Arbeitsgemeinschaft Additive Manufacturing sprachen über AM-Technologien zur Herstellung metallischer Bauteile, den gegenwärtigen Stand der Werkstoffentwicklung sowie den Workflow bei der additiven Produktentwicklung. Moderiert wurde das Symposium von Rainer Gebhardt, der im VDMA die AG Additive Manufacturing betreut.
Rudolf Derntl, Geschäftsführer der Hermle Maschinenbau GmbH in Ottobrunn, erläuterte zum Beginn anschaulich das von Hermle entwickelte MPA-Verfahren (Metall Pulver Auftrag). Bei diesem Verfahren wird ein mit Metallpulver-Teilchen angereicherter Gasstrom in einer Laval-Düse so stark beschleunigt, dass er mit dreifacher Schallgeschwindigkeit auf das Werkstück auftrifft. Energieträger für die Beschleunigung ist überhitzter Wasserdampf. Beim Auftreffen verbinden sich die Teilchen unter plastischer Verformung und einer Temperaturerhöhung auf maximal 300 °C dauerhaft mit dem Grundwerkstoff. Das Verfahren ermöglicht den Aufbau von Werkstücken aus unterschiedlichen metallischen Werkstoffen, wobei auch verschiedene Metalle zugleich in den Pulverstrom gegeben werden können. Ziel der Entwicklung war es, den subtraktiven Fräsprozess mit einer additiven Technologie aufzuwerten, um die Fertigung von bis dato nicht herstellbaren Werkstücken zu ermöglichen. Damit können z. B. auf beliebigen Formen konventionell Kühlkanäle gefräst werden, die dann mit einem wasserlöslichen Füllstoff ausgefüllt und über das MPA-Verfahren mit einer Deckschicht versehen werden. Anschließend wird der wasserlösliche Füllstoff ausgespült. Das Verfahren vereint so die Stärken additiver (kinetisches Kompaktieren) und subtraktiver (Fräsen) Verfahren. Die Auftragsraten liegen oberhalb 200 Kubikzentimeter pro Stunde.
Ein noch relativ junger Player im Pulverbett-Segment ist die Firma O.R. Lasertechnologie aus Dieburg, deren Technologie und Anlage von Markus Wolf vorgestellt wurden. Das Unternehmen kommt ursprünglich aus der Laserschweißtechnik und bietet Pulverbett-Anlagen mit Bauplattform-Größe Ø 100 mm x Höhe 100 mm, Laserleistung 250 W und Laser-Spotgröße 40 µm an. Der Beschichtungsarm zum Auftrag der jeweils nächsten Pulverschicht arbeitet rotatorisch. Das fertige Bauteil muss von der Bauplattform abgetrennt werden, bei entsprechender Wahl der Stützstrukturen ist das jedoch auch durch einfaches manuelles Herausdrehen möglich. Eine Besonderheit der O.R.-Anlage ist die Freiheit im Hinblick auf die Werkstoff-Parametersätze. So stellt O.R. Lasertechnologie die Parametersätze zu jedem neu qualifizierten Werkstoff kostenlos zur Verfügung. Dadurch wird die Anlage im Laufe der Zeit multifunktioneller. Sinnvolle Schichtdicken für den Druck beginnen bei 25 µm, die Positioniergenauigkeit der Plattform beträgt 1 µm.
Über die Metallpulver-Herstellung berichtete Dr. Johannes Schmid von Aubert Duval/Erasteel, die fast zwei Drittel ihres Umsatzes im Bereich Luft- und Raumfahrt machen. Da in dieser Branche die Nachfrage nach additiven Verfahren steigt, entstand bei Aubert Duval/Erasteel der Wunsch, selbst in die Pulverherstellung einzusteigen. Inzwischen werden Stahl- und Nickel-Basis-Pulver an verschiedenen Standorten in Europa hergestellt. Bei der VIM Gas Verdüsung läuft der gesamte Prozess von der Verdüsung bis zur Verpackung unter Schutzgas ab. Ergebnis sind hochreine Metallpulver für AM, die auch die entsprechende Lagerfähigkeit aufweisen. Neu ist eine Pilotanlage für Titan, da dieser Werkstoff mehr und mehr von der Luftfahrtbranche nachgefragt wird. Wichtig für AM ist, dass die Pulverteilchen sehr sphärisch ausfallen, nur wenige Satelliten haben und sich zur Gewährleistung der Fließfähigkeit in einem definierten Größenbereich befinden (35 bis 60 µm). Die erzeugten Pulver liegen zunächst in einer Gaußverteilung vor. Abhängig vom Anwendungsfall muss dann der kleinste und der größte Anschnitt siebtechnisch entfernt werden. Je größer der entfernte Anteil, desto teurer ist das Pulver. Während man in der Vergangenheit auf klassische Legierungen zurückgegriffen hat, bezieht man aktuell auch ungewöhnliche Legierungen mit ein. Künftig sind dann gänzlich neue Legierungen denkbar, für die es bisher noch gar keine Anwendungen gibt. Ziel sind dabei maßgeschneiderte Eigenschaften für das jeweilige AM-Verfahren.
Der Geschäftsführer von DMG Sauer und ReaLizer, Patrick Diederich, gab einen Einblick zur innovativen Herstellung von AM-Bauteilen für Industrieanwendungen. Dazu reichte er zunächst zwei Musterwerkstücke herum, die eindrucksvoll die Gewichtseinsparung und die Integration von Kühlkanälen durch additive Verfahren demonstrierten. Während die von ReaLizer angebotenen Pulverbett-Maschinen eher für kleinere und filigrane Bauteile mit hoher Funktionsintegration in Frage kommen (Anwendungen z. B. in der Medizintechnik oder für reaktive Werkstoffe), bedient Fa. Sauer mit den Pulver-Düse-Anlagen den Markt für größere Bauteile, die bis hinein in Branchen wie den Automobilbau Anwendung finden. Die Herstellung von Zahnkronen stellt im Grunde die weltweit erste Branche dar, die inzwischen vollständig auf Additive Manufacturing im Pulverbett setzt. Ausnahme ist nur die Bundesrepublik Deutschland, da die hiesigen Krankenkassen noch nicht ihr Okay zum Pulverbett-Verfahren gegeben haben. Das Pulver-Düse-Verfahren lässt sich auch in eine Drehmaschine integrieren. Mit einem solchen Aufbau wurden bereits Raketendüsen für das Unternehmen SpaceX gefertigt, die bereits bei Raketen-Tests praktisch eingesetzt wurden. Problem ist heute weniger die technische Machbarkeit als vielmehr die Tatsache, dass sich noch zu wenig „additives Denken“ in den Köpfen der Konstrukteure wiederfindet. Erst mit diesem können die Potenziale von AM vollständig gehoben werden.
Zu den Aktivitäten von Fa. Trumpf berichtete Frank Nachtigall, Branchenmanager für den Bereich Additive Manufacturing. Die Lasertechnik macht bei Trumpf inzwischen 30 Prozent des Umsatzes aus. Trumpf liefert die Laser und Laserschweißköpfe vielfach an Integratoren, die diese in eigene Maschinen einbauen. Der erste Vorstoß von Trumpf in den Bereich Additive Manufacturing erfolgte 2003 zu früh für den Markt. Erst 2014 sei der Markt so weit gewesen, dass man mit der TruPrint 1000 wieder einsteigen konnte. Neben der TruPrint Reihe werden auch Lösungen zum Laserauftragsschweißen angeboten, allerdings über einen Drittanbieter. Für den Erfolg von AM ist ein Denken in neuen Systemgrenzen erforderlich. Beispiele dafür sind hybride Bauteile, die aus einem konventionell bearbeiteten Teilstück und einem daran angebrachten (aufgeschweißten) AM-Bauteil bestehen. Mit der TruPrint 3000 hat Trumpf eine weiterentwickelte Maschine im Angebot. Sie arbeitet nach dem Wechselzylinder-Prinzip, wodurch sich die Produktivität erhöht. Ein Doppeldeckel-Verschluss verhindert den Kontakt des Bedieners mit dem Pulver beim Bauteilwechsel. Die Maschine kann bis zu 4000 Stunden durchgehend betrieben werden ohne Pulverwechsel/Schutzgasneuflutung. Zukünftige Optimierungen betreffen den Einsatz von bis zu drei unabhängigen Lasern, die auch zu einem einzigen Spot gebündelt werden können. Zudem ist eine Pulver-Vorheizung auf bis zu 500 °C möglich. Die Pulverbett-Überwachung ist bereits Realität, eine eigene Schmelzbad-Überwachung befindet sich in der Entwicklung.
Zur digitalen Prozesskette berichtete Helmut Zeyn von der Siemens Industry Software GmbH, Hamburg. Neben der Bereitstellung von Software-Lösungen hat Siemens auch eigenes Interesse am Thema AM. Als Beispiel können Blades für eine Gasturbine dienen, die additiv hergestellt sind und integrierte Kühlkanäle aufweisen. Siemens nutzt die Fluid-Simulation, um eine optimale Kühlkanalform zu entwickeln. Mittels AM wird dann im Grunde das Metallbauteil um die optimierte Kühlkanalform herum aufgebaut. Ziel ist für Siemens ein durchgängiges System von der Idee bis hin zur Fertigung mit nur einem Datenformat. Softwareseitig stehen für die Modellierung verschiedenste Gitterstrukturen zur Gewichtseinsparung zur Verfügung. Gewichts- und Topologie-Optimierungen sind direkt in der Konstruktions-Umgebung (Baugruppe) möglich. Anschließend wird das Modell vorbereitet und an die Additiv-Maschine übergeben. Gerade beim 3D-Druck von Metallen wird viel Energie in das Bauteil eingebracht. Um dem damit einhergehenden Bauteilverzug zu begegnen, beschreitet Siemens den Weg einer Vorab-Simulation unter Berücksichtigung der Parameter der Maschine. Momentan erzielt man damit eine Abweichung vom realen Verzug von wenigen Prozent. Laut Kundenstimmen von Siemens können die Kosten für die Nachbearbeitung bis zu 40 Prozent der Bauteil-Gesamtkosten betragen. Daher macht es Sinn, die Nachbearbeitung von Anfang an mit einzubeziehen (alles in einem System und mit einem Datensatz).
Bild: Torsten Bell
796
FollowerEMO-Symposium beleuchtet Chancen und Perspektiven der additiven Fertigung
25Sep. 2017
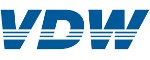
MarketingVerein Deutscher Werkzeugmaschinenfabriken e.V. am 25. September 2017 um 19:34 Uhr
